Anwendungsbeispiel: Verpackungsmaschinen als Hauptverbraucher
Kraft Foods Deutschland GmbH, Berlin
Das Werk Berlin von Kraft Foods dürfte die größte Kaffeerösterei der Welt sein. Druckluft wird überall gebraucht, von den Silos für den Rohkaffee über die Rösterei und die Mühlen bis hin zu den Verpackungsanlagen.
Die Statistik für das Jahr 2001 weist eine Liefermenge der Kompressorstation von 32 Mio. m3aus. Zahlen wie diese werden seit dem vergangenen Jahr nicht mehr geschrieben. Seitdem die Druckluftströme der drei Anlagenbereiche, auf die rund 65% des Gesamtverbrauches entfallen, durchgängig überwacht werden, geht man von einer durchschnittlichen Verbrauchsreduzierung von 30% aus. Die Minimierung der Leckageverluste und zwei neue drehzahlgeregelte Kompressoren, die zwei vorhandene ersetzt haben, erlaubten die Absenkung des Betriebsdruckes um 1 auf 6,2 bar.
Die Pilotinstallation, die auf Durchflussmessungen nach dem kalorimetrischen Prinzip basiert, beweist eindringlich, dass sich die Kosten der Druckluft dramatisch senken lassen.
Durchflussmessungen nach dem kalorimetrischen Prinzip:
Das Konzept dazu, vertreten von den Spezialisten Postberg und Otto, ist bei Kraft Foods auf vielfältige Weise bestätigt worden. Die Kernpunkte: Durchflussmessungen an allen entscheidenden Stellen des Versorgungsnetzes (Messebene 2 bis 4) sind der Schlüssel für die effiziente Druckluftnutzung. Die gewünschte Messgenauigkeit ist in den vorgegebenen Messbereichen mit Sensoren zu erreichen, die nach dem kalorimetrischen Prinzip funktionieren und definiert in die Rohrleitungen eingebaut werden. Die Durchflussraten können nach Art der Stromzähler direkt vor Ort abgelesen, per Datenleitung an einen Zentralrechner oder via Datenfernübertragung an ein werksunabhängiges Controlling-Unternehmen weitergeleitet werden. Bei Kraft Foods werden alle Varianten verwirklicht. Die schrittweise Umsetzung des gesamten Druckluftprojektes wurde sorgsam geplant.
Nicht zuletzt, um auf der Lernkurve nach oben keine unliebsamen Rückschritte hinnehmen zu müssen. Bis heute sind nur die drei Gruppen von Großverbrauchern (Verpackung, Palettierung und Mühlen) Gegenstand der Messinstallation, der Auswertung ihrer Messungen und der vollzogenen Beseitigung festgestellter Leckagen.
Ohne Lecks ging der Druckluftverbrauch der ersten von ihnen befreiten Verpackungsanlage um über 40% von 110 auf etwa 60 m3/h zurück. Inzwischen werden alle zwölf Verpackungslinien überwacht, für die die beseitigten Leckverluste mit durchschnittlich 30% angenommen werden.
Weitere Details zum Anwendungsbeispiel finden Sie im Fachartikel "Drucklufttechnik: Druckluftverbrauch eines ganzen Werks unter Kontrolle"
Anwendungsbeispiel: Energie-Einspargarantie „EnerGarant®“
Privatmolkerei Naarmann, Neuenkirchen/Münsterland
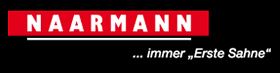
Als die münsterländische Privatmolkerei Naarmann im Jahre 2007 einen Werksstudenten beauftragte, eine Aufnahme des über Jahrzehnte „organisch“ gewachsenen Druckluftsystems ihrem Betrieb vorzunehmen, so ging damit die Absicht der Geschäftsführung einher, zum einen eine verbesserte Prozesssicherheit im Bereich der verwendeten Drucklufttechnik zu erzielen, und zum anderen den Verbrauch dieses in der Produktion besonders teuren Mediums deutlich zu reduzieren, um die hohen Stromkosten zu senken.
Zu diesem Zweck wurde die Firma Postberg + Co GmbH, Kassel, eingebunden, um mit Hilfe einer umfassenden messtechnisch gestützten Analyse den Ist-Zustand der Druckluftanlagen zu ermitteln, auf dessen Basis später ein Optimierungskonzept entwickelt werden sollte, welches Fa. Naarmann dann in Einzelschritten und in Eigenregie umsetzen wollte. Für die fortlaufende Überwachung der selbst durchgeführten Verbesserungsmaßnahmen sollte die Messtechnik von Fa. Postberg verwendet werden.
Neben der Offerte über die Druckluftmesstechnik bot Postberg zusammen mit seiner Partnerfirma INS InfraNetServ GmbH, Lippstadt, der Fa. Naarmann jedoch zusätzlich an, auf Basis einer Energie-Einspargarantie ein Konzept zur umfassenden Revision der Drucklufttechnik zu entwickeln, welches nicht nur die Erneuerung verschiedener Bereiche der Druckluftanlagen beinhaltete, sondern zugleich auch die Redundanz weiter verbessern ebenso wie zur vollständigen und fortlaufenden Überwachung der Druckluftqualität beitragen sollte. Ferner sollte in weiteren später folgenden Einzelschritten geprüft werden, welche sonstigen energetischen Optimierungen im Unternehmen möglich wären und gleichfalls auf Basis der garantierten Einsparung umgesetzt werden könnten.
Weitere Details zum Anwendungsbeispiel finden Sie im Fachartikel"Drucklufttechnik: Energie-Einspargarantie".